Build, enhance, maintain.
Automation teams have multiple priorities pulling them in different directions at all times. Aligning those priorities and incoming requests to a logical automation pipeline can be a tricky science that leaves many of us scratching our heads, unintentionally stalling work, or stuck in a hamster wheel of building, enhancing, maintaining, and trying to keep up with demand with no business assessment or master plan in mind. I’m exhausted just thinking about it!
Which new opportunities or enhancement requests should be addressed first? How can you consider variables like time, effort, and ROI to calculate prioritization? Today, I want to introduce you to a secret weapon—a metrics tracking system you can leverage to capture essential data from the beginning, make smart decisions about automation priorities, and set your team up for success downstream.
Enhancement vs. New Automation
If you’re in the Start phase of your automation program—POCing your first use case and tackling those initial low-hanging fruit opportunities—everything is about new builds. Once you’ve established automation’s credibility in your organization and gained trust from a few groups and stakeholders, inevitably, you’ll see them come back to request an enhancement on an automation you created for them.
Enhancing an automation can mean changing how it functions or adding a new capability to streamline the process further and capture additional value. Not a bad idea! If you can improve it, and it’s less work than tackling a new automation request in your pipeline, why not honor that enhancement request first? Well, deciding to tackle an enhancement instead of starting a new build or tending to maintenance needs is not a given. You need evidence to inform and support your decision on what gets first priority, especially if an executive requested the enhancement and stressed its crucial strategic value. That’s hard to say no to. Having detailed metrics from your existing automations will arm you with evidence to justify whether the enhancement or new build will drive more business value and should, therefore, be prioritized.
Work Item Tracking
Different data spell “success” to different stakeholders. For a new automation request, most companies have a system in place for assessing the potential business case and the level of effort it will take and then determining how to prioritize it. But how do you leverage your data to determine whether an enhancement request should be completed over a new automation request? Work Item Tracking gives the enhancement business case detail you need to compare to the new automation request and prioritize accordingly.
In the simplest terms, Work Item Tracking is a report that documents anything an automation touches. It’s a complete data exhaust of a given automation, and it can be done very simply in Excel. The benefit of Work Item Tracking is that it allows you to provide meaningful data to each stakeholder who may request it.
Let’s look at an example...
Consider an automation that picks up an invoice for an order and triggers a shipment of goods to a customer. It's part of an extensive business process where humans do a bunch of work upfront, then, instead of doing all the shipping work themselves, an automation takes over. The automation records when it took action as the ship date and details outcomes in Error Notes, including when it couldn't process things because of a business rule. In this example, it has noted exceptions for exceeding a dollar amount threshold that requires human intervention and shipping destinations to Canada that require use of a different shipping system.
Here is a small representation of what that output could look like in Work Item Tracking:
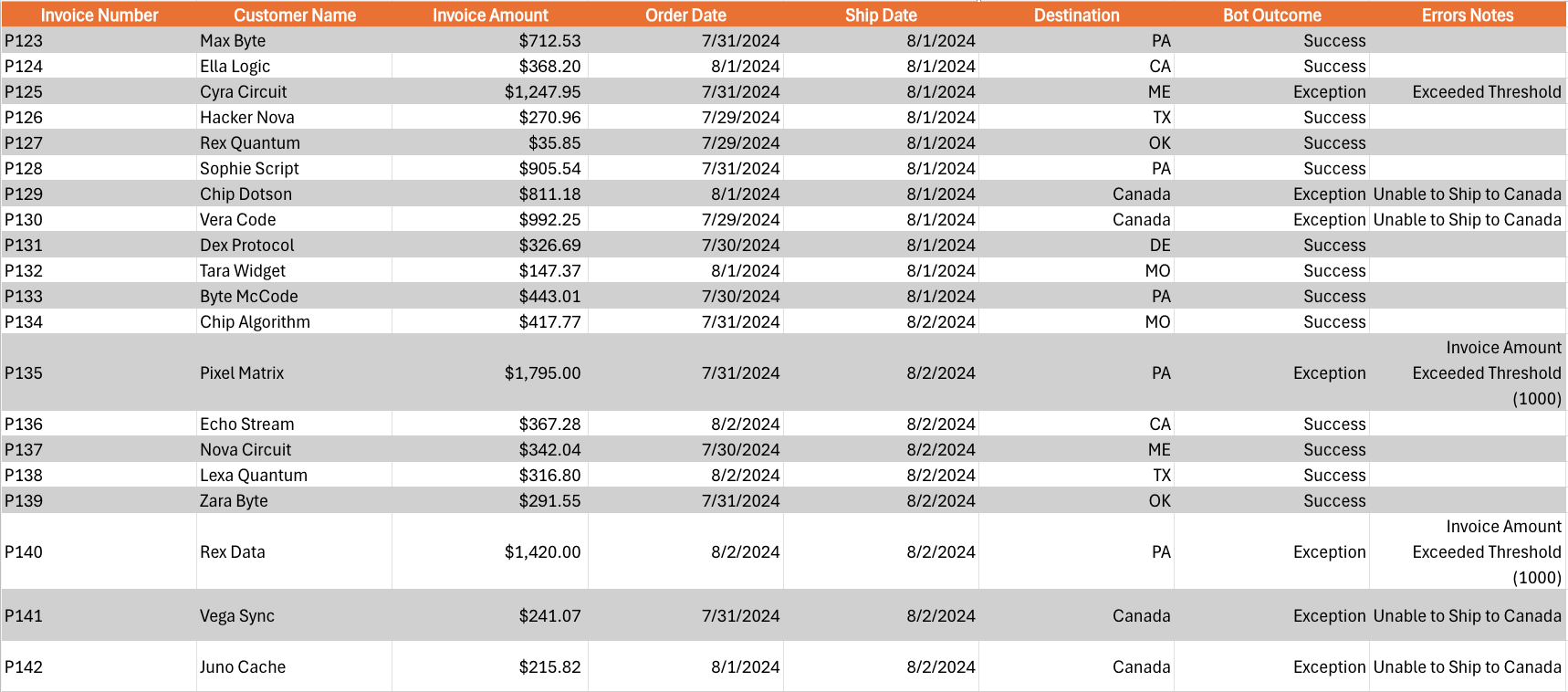
So, what metrics can you extract from this? The answer is Everything! You can provide operational metrics about output to department heads, reliability and error rate to IT Managers, and financial information about time saved to executives. You can examine where your customers are coming from, customer wait times, the average time to ship, and so much more. And while the automation might be creating redundant data because the systems these tools are interacting with might have disparate data on their own, the point is: If you build this into your process at the beginning, it doesn’t add much complexity from a development standpoint, and you’ll have all of the information that you could ever produce from then on. So, when any request for metrics comes in, you have answers all in one place.
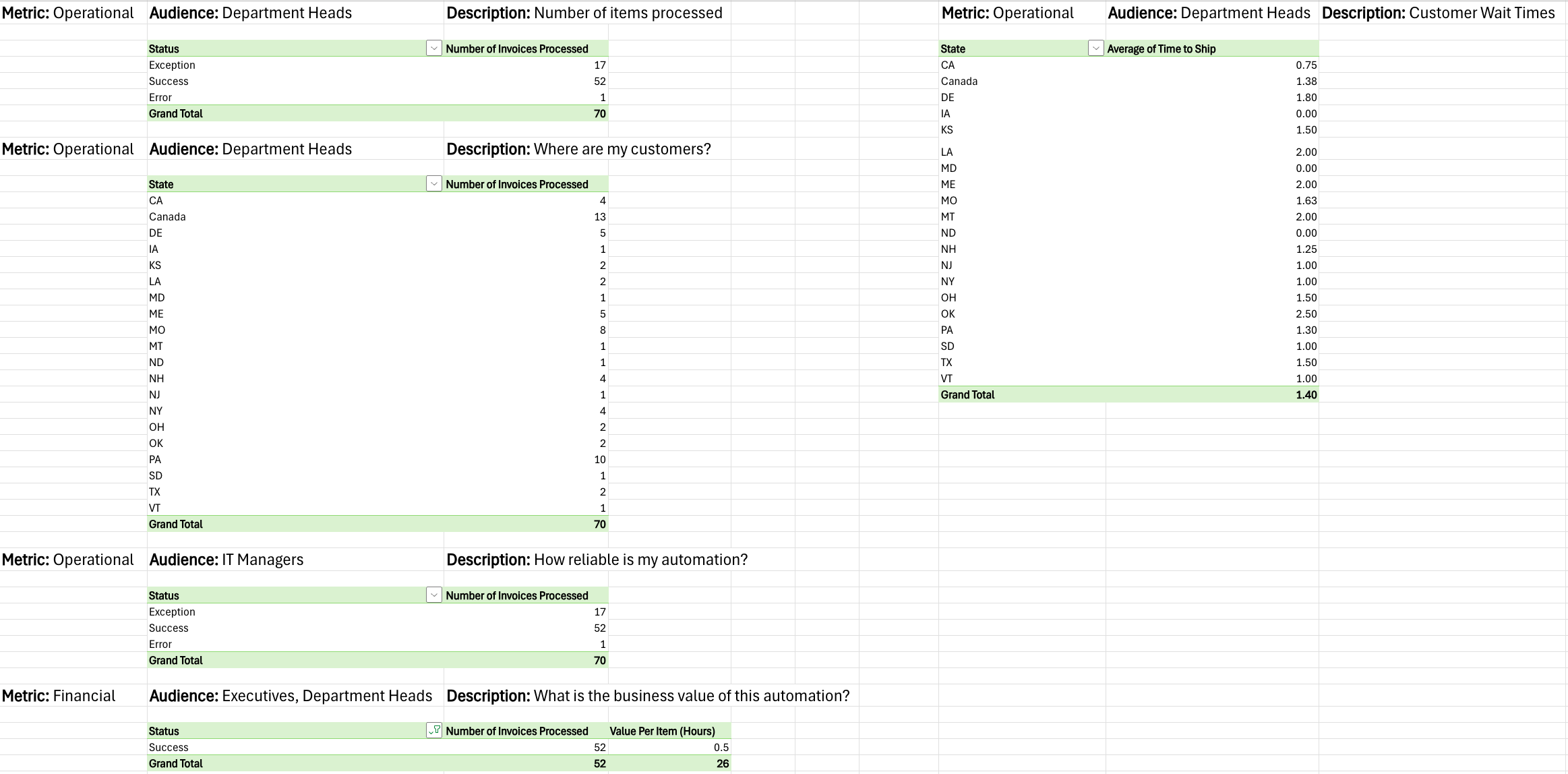
Enhancement vs. New Automation Revisited
Now, to come full circle on the enhancement vs. new build predicament: let’s say this group asks you to enhance the above automation so it can ship to Canada. At the same time, you have another request to develop a new automation that will help employees monitor inventory.
Thanks to Work Item Tracking, you can quickly reference the data to discover there would be an 18.57% lift in processing, equating to an additional 6.5 hours of time saved. And given that it’s just an enhancement, the estimated time to complete is quite quick. Compare that knowledge to the new automation request that would potentially save 12 hours, but would be twice the amount of work. We now have evidence and confidence that, in this case, the enhancement request is the quicker win that will deliver more value for the same amount of effort.
Metrics Support Your Continued Success
I’ve witnessed that the philosophy with many customers early in their programs tends to be “the returning customer gets priority, period.” And I get it! You want to reciprocate loyalty to your early business users, especially if they become an Automation Champion for your program. However, there comes a point as your program matures and your team starts to feel the pull in all directions when a system like Work Item Tracking becomes essential. People—especially high-level stakeholders and loyal business users—like instant gratification. Work Item Tracking provides concrete data to support your prioritization rationale to any stakeholder from a business value perspective. That’s hard to argue with when you have to tell someone why their request may have to wait.
Enhancement vs. new automation analysis aside, Work Item Tracking is, in my opinion, the best and most comprehensive way to measure the value of an automation, with meaningful metrics available to share with any stakeholder at the drop of a hat. Where’s the downside in that?